De keramische spuitgiettechnologie, ook wel CIM genoemd, is een belangrijke tak van de poederinjectiegiettechnologie (PIM). Het is ook ontwikkeld op basis van de relatief volwassen polymeer spuitgiettechnologie. Omdat het producten met complexe vormen kan produceren en de voordelen heeft van hoge maatnauwkeurigheid, glad oppervlak en lage kosten, heeft het zich snel ontwikkeld.
Overzicht van keramisch injectieproces
Keramiek wordt grofweg onderverdeeld in dagelijkse keramiek en industriële keramiek. Hier introduceren we voornamelijk industrieel keramiek. Er zijn vele soorten industrieel keramiek, de meest gebruikte zijn aluminiumoxide, zirkonia, siliciumcarbide, siliciumnitrideBoornitride, enz. Industriële keramiek heeft over het algemeen een hoge hardheid, slijtvastheid en bestendigheid tegen hoge temperaturen, evenals een hoge weerstand tegen corrosie, zodat ze op grote schaal worden gebruikt in de elektronica, machinebouw, chemische industrie, ruimtevaart en andere industrieën.
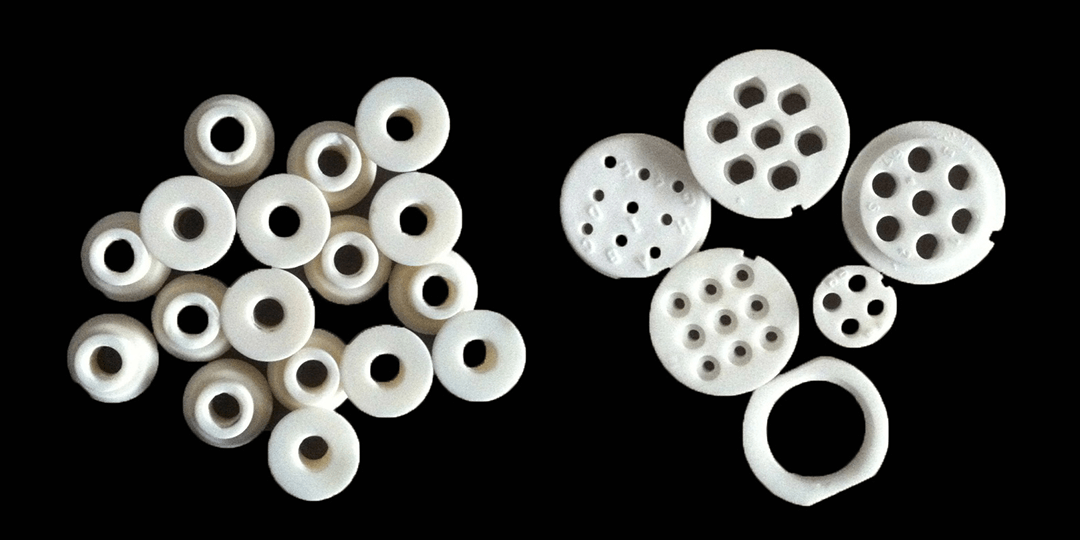
Er zijn over het algemeen drie gietmethoden voor industriële keramiek. De eerste is de gietmethode, de tweede is de droge persmethode en de derde is de injectiemethode. Hier introduceren we voornamelijk keramisch spuitgieten (Ceramic Injection Molding CIM). De spuitgietprocessen voor verschillende soorten keramiek zijn vergelijkbaar en worden hieronder gezamenlijk keramisch spuitgieten genoemd.
Spuitgieten van keramiek is een methode om keramische onderdelen met complexe vormen en uitstekende eigenschappen te maken door keramisch poeder te mengen met organische bindmiddelen, te malen, te mengen, te granuleren, te voeden, te spuitgieten, te ontvetten en te sinteren. Vormtechnologie. Deze technologie heeft de voordelen van een hoge vormnauwkeurigheid en een hoge efficiëntie, dus wordt het op grote schaal gebruikt in de keramische sector.
Hieronder volgt een gedetailleerde uitleg van deze processen:
Poeder malen: Maal het oorspronkelijke keramische poeder om de vloeibaarheid en uniformiteit te verbeteren, wat gunstig is voor het latere spuitgietproces.
Intern mengen van keramisch poeder en kunststof bindmiddel: Meng het gemalen keramische poeder met een geschikte hoeveelheid bindmiddel en bereid vloeibare keramische injectiegrondstoffen voor door middel van mengen, mengen, drogen en andere processen in een interne mixer. Voor spuitgieten omvatten de lijmen PP, PE, PA, POM, enz.
Injectie van voeding: Injecteer de keramische injectieslurry in de matrijs en door processen zoals druk houden, koelen en ontvormen worden keramische onderdelen met een bepaalde vorm en grootte verkregen.
Ontvetten: Door verhitting of andere fysische en chemische methoden wordt de lijm van de keramische onderdelen verwijderd om een groen embryo met een basisvorm te verkrijgen.
Sinteren: Het groene embryo wordt bij hoge temperaturen gesinterd om het te verdichten en het uiteindelijke keramische product te vormen.

Spuitgietmachines selecteren
De lijm kan gemaakt zijn van verschillende grondstoffen, dus bij het selecteren van de machine, vooral de schroef, moet rekening worden gehouden met de kenmerken van de keramische grondstof en de lijm.
Schroef- en vatkeuze: Hoewel verschillende soorten keramiek na het sinteren sterk verschillen in hardheid en andere eigenschappen, zijn ze in de grondstoffase vóór het sinteren in principe hetzelfde. Ze lijken in principe erg op modder. Over het algemeen zal het aandeel bindmiddel 20% niet overschrijden. Deze keramische materialen veroorzaken veel slijtage aan de schroeftrommel. Bij de keuze van schroeven kun je het beste kiezen voor schroeven van snelstaal of andere hardmetalen materialen en lopen met inwendige hulzen van een nikkellegering. De compressieverhouding van de schroef wordt meestal geregeld tussen 2,0 en 2,3, de lengte-diameterverhouding van de schroef is ongeveer 22:1, de voorkant van de schroef is uitgerust met een open mengkop en de kopflens moet een ontluchtingsgat toevoegen.
Vermogenselectie: In tegenstelling tot gewoon spuitgieten zijn er na keramisch spuitgieten ontvettings- en sinterprocessen, vooral sinteren. Als de interne spanning van het geïnjecteerde keramische groene embryo groot is, zal de vervorming tijdens het sinteren ook relatief groot zijn. Daarom is het kiezen van het juiste vermogen op basis van de wanddikte van het product een belangrijke stap. Over het algemeen kiezen we een machinevermogen dat groter is dan het werkelijk benodigde vermogen om een hogere injectiesnelheid te verkrijgen. Wat betreft de injectiedruk: vanwege de slechte vloeibaarheid van de keramische slurry is een relatief grote injectiedruk vereist.
Selectie van machinetonnage: Het soortelijk gewicht van verschillende keramische materialen varieert sterk, dus het zou wetenschappelijker zijn om het injectievolume te gebruiken om het type te selecteren. Aangezien het injecteren van keramiek niet veel klemkracht vereist, kunnen basisproducten worden geproduceerd zolang de mal omlaag kan en het injectievolume voldoende is (de verhouding tussen het injectievolume van de machine en het productvolume ligt het best tussen 3:1 en 2:1).
Selectie van machinemerken: Er zijn niet veel volwassen machinemerken voor keramische injectie. Over het algemeen worden vooral merken als Rigang, Arburg, Jibo en Haïtiaan gebruikt.
Vereisten voor schimmel
Eisen aan het staal van de matrijskern: Ook vanwege de abrasiviteit van keramiek moet het materiaal voor de matrijskern gemaakt zijn van gelegeerd staal met een hogere hardheid.
Vormuitlaat: Keramische injectie wordt gebruikt om poriën in het product te voorkomen, die na het sinteren kunnen leiden tot schrapen. Omdat voor lijmen vaak POM en andere grondstoffen worden gebruikt die meer gas genereren, zijn de uitlaatvereisten voor de mal relatief hoog. Tegelijkertijd, omdat de injectiesnelheid niet te hoog kan zijn, moet de uitlaatgroef zo ver mogelijk aan het uiteinde worden geplaatst waar de lijm het langzaamst reist.
Vormagent: Vanwege de slechte vloeibaarheid van keramische materialen is het over het algemeen niet aan te raden om een hete runner te gebruiken, en de diameter van de koude runner moet zo groot mogelijk zijn om de stroom van keramische grondstoffen te vergemakkelijken.
Matrijspoort: Net als bij de twee bovenstaande punten moet de matrijspoort over het algemeen groter zijn om de stroom van keramische grondstoffen en de behoefte aan uitlaatgassen te vergroten.
Het aantal vormholten: Aangezien de meeste keramische producten een bepaalde grootte hebben en het keramische groene embryo na het gieten nog een sinterstap ondergaat, is de grootte van producten met een groot aantal holtes vaak moeilijk te controleren, dus wordt over het algemeen een plan met een klein aantal gaten gebruikt.

Procesaanpassing
Injectiesnelheid: In het keramische injectieproces kan een te hoge injectiesnelheid gemakkelijk defecten zoals poriën en straallijnen veroorzaken, terwijl een te lage snelheid tot problemen zoals laslijnen kan leiden. Daarom wordt over het algemeen een proces van langzaam vullen door de poort en vervolgens vullen met een gemiddelde snelheid gebruikt. .
Injectiedruk: In tegenstelling tot gewoon kunststof spuitgieten kan een te hoge injectiedruk interne spanningsproblemen veroorzaken. Door de slechte vloeibaarheid van keramiek ontstaan er grote interne spanningen op bepaalde knikposities tijdens het injectieproces. Het gegoten groene embryo heeft misschien geen problemen, maar als het eenmaal gesinterd is, zullen deze posities grotere interne spanningen veroorzaken. Vervorming, met productafval tot gevolg. Probeer daarom bij het injecteren een lagere injectiedruk te gebruiken. Hetzelfde geldt voor de houddruk.
Smelttemperatuur: Een hogere materiaaltemperatuur is gunstig voor het elimineren van productstress, maar een te hoge materiaaltemperatuur veroorzaakt het vrijkomen van gas en produceert poriën en andere defecten, vooral bij keramische grondstoffen die POM met een grote hoeveelheid gas als bindmiddel gebruiken. .
Vormtemperatuur: Een hogere matrijstemperatuur is uiteraard gunstig voor het verbeteren van de vloeibaarheid van keramische grondstoffen in de matrijs, waardoor de interne spanning van het product afneemt. Een te hoge matrijstemperatuur kan er echter voor zorgen dat de kunststof die als bindmiddel wordt gebruikt naar het oppervlak drijft dat in contact komt met de kern van de matrijs, wat de kwaliteit van het product na het sinteren kan aantasten.
Openingssnelheid van de mal: Omdat de fysische eigenschappen van het pasgevormde keramische groene embryo nog relatief kwetsbaar zijn, moet de openingssnelheid van de mal relatief laag zijn en moeten trillingen zoveel mogelijk worden beperkt. Hetzelfde geldt voor de robotverwijdering.
Als u industriële keramische producten nodig hebt, neem dan gerust contact met me op. 0086-17702411651