96% Alumina Ceramic Substrate:Properties, Applications, and Market Trends in Industrial Ceramics
Introduction
96% alumina ceramic substrate, a high-performance material renowned for its thermal stability, electrical insulation, and mechanical strength, has become indispensable in modern industries. With a composition of 96% aluminum oxide (Al₂O₃) and 4% additives, this substrate balances cost-effectiveness and performance, making it a cornerstone in electronics, automotive, aerospace, and energy sectors. This article explores its unique properties, manufacturing innovations, key applications, and evolving market dynamics.
1. Key Properties of 96% Alumina Ceramic Substrate
-
– Thermal Stability: With a high melting point (~2072°C) and low thermal expansion coefficient (~7×10⁻⁶/°C), it excels in high-temperature environments, such as aerospace engines and semiconductor equipment.
– Electrical Insulation: Its low dielectric loss and high resistivity make it ideal for high-voltage applications, including power electronics and circuit substrates.
– Mechanical Durability: High hardness (Mohs 9) and flexural strength (≥500 MPa) ensure resistance to wear and mechanical stress, suitable for abrasive environments.
– Chemical Resistance: Stable in acidic, alkaline, and corrosive conditions, extending its lifespan in harsh industrial settings.2. Advanced Manufacturing Techniques
The production of 96% alumina substrates involves precision processes to achieve uniform density and surface smoothness:
– Slurry Preparation: Raw Al₂O₃ powder (α-phase ≥95%, Na₂O <0.1%) is mixed with binders and plasticizers to form a homogeneous slurry.
– Forming Methods:
– Tape Casting: A cost-effective method for thin substrates, using optical-grade PET/PVA films to ensure surface smoothness.
– Isostatic Pressing: Enhances density and minimizes defects, critical for high-reliability applications like semiconductor packaging.
– Sintering: Controlled high-temperature sintering (1500–1600°C) optimizes microstructure and mechanical properties.Recent innovations, such as Guangdong Huanbo’s patented optical-grade film-assisted tape casting, have improved surface finish (Ra <0.1 μm) and production efficiency.
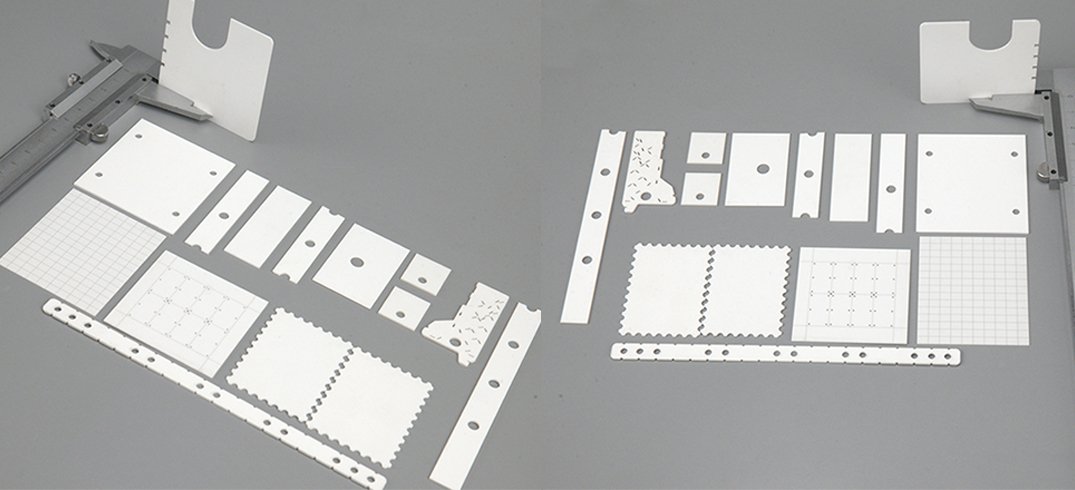
3. Major Applications Across Industries
Electronics & Semiconductors
– Power Modules: Used in IGBT packaging for electric vehicles (EVs) due to its electrical insulation, though limited by lower thermal conductivity compared to AlN.
– Circuit Substrates: Supports high-frequency communication devices in 5G infrastructure.
Automotive
– Sensor Packaging: Withstands extreme temperatures and vibrations in LiDAR, cameras, and radar systems.
– LED Lighting: Efficient heat dissipation for high-power automotive LEDs, reducing thermal degradation.
Aerospace & Energy
– Thermal Management: Used in satellite components and nuclear reactors for its stability under radiation and high heat flux.
4. Market Trends and Competitive Landscape
– Growth Drivers: The global market is projected to grow at a CAGR of ~10–15%, fueled by demand from EVs, renewable energy, and 5G technologies.
– Key Players: Leading manufacturers include CoorsTek, Kyocera, and Rogers Germany, while Chinese firms like Zhongjiang Keyi (recently securing ¥100M Series A funding) are expanding production for EV and photovoltaic sectors.
– Regional Insights: China dominates production, accounting for ~40% of the global supply, driven by government support for advanced ceramics.
5. Challenges and Future Outlook
– Technical Limitations: Lower thermal conductivity (24–28 W/m·K) compared to AlN (170–200 W/m·K) restricts its use in ultra-high-power devices.
– Market Competition**: Price wars and overcapacity have emerged due to rapid industry expansion, urging manufacturers to innovate in cost-efficient processes.
– Emerging Opportunities**: Research focuses on doping Al₂O₃ with MgO/CaO to enhance thermal performance, while hybrid substrates (e.g., Al₂O₃-Cu) gain traction in EV power modules.
Conclusion
96% alumina ceramic substrate remains a versatile and economical choice for industries demanding reliability under extreme conditions. As technology evolves, advancements in material purity and manufacturing techniques will further solidify its role in next-generation applications. For manufacturers, prioritizing R&D and niche markets (e.g., high-precision optics) will be key to sustaining growth amid competitive pressures.
Contact Us:https://vhandy.com/contact-us/