Sustratos cerámicos se utilizan ampliamente en campos como la electrónica de potencia, los envases electrónicos, la microelectrónica híbrida y los módulos multichip debido a su excelente conductividad térmica y estanqueidad al aire. La alúmina es actualmente el material de sustrato cerámico más utilizado. No sólo tiene una alta resistencia mecánica, aislamiento, resistencia a altas temperaturas, buena estabilidad, rendimiento de alto coste, buena resistencia al choque térmico y puede formar una soldadura sellada con metal. Con ventajas como su madura tecnología de fabricación y procesamiento y su bajo coste, se ha utilizado ampliamente en circuitos de película gruesa, circuitos de película fina, circuitos híbridos, componentes multichip, módulos IGBT de alta potencia y otros campos. También es el material de sustrato cerámico más utilizado en la actualidad.
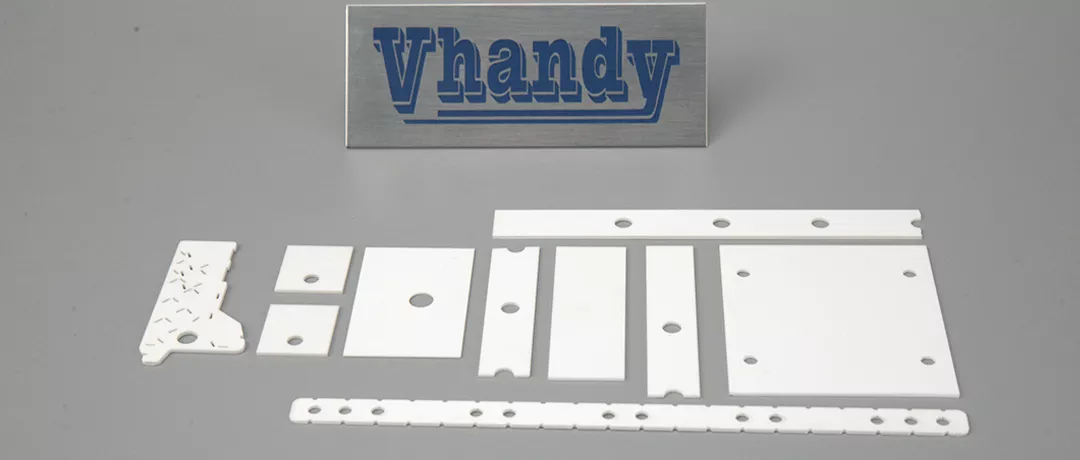
Tipos de cerámica de alúmina
Las cerámicas de alúmina pueden dividirse en dos tipos en función de su pureza: las de tipo alto puro y las de tipo ordinario.
① Alúmina de gran pureza
La cerámica de alúmina de alta pureza es un material cerámico con un contenido de Al2O3 superior a 99,9%. Dado que su temperatura de sinterización es de hasta 1650~1990°C y la longitud de onda de transmisión es de 1~6μm, generalmente se convierte en vidrio fundido para sustituir a los crisoles de platino, utilizando su capacidad de transmisión de luz y su resistencia a la corrosión por metales alcalinos y se utiliza como tubo de lámpara de sodio; en la industria electrónica, puede utilizarse como sustrato de circuito integrado y material aislante de alta frecuencia.
② Cerámica de alúmina ordinaria
La cerámica de alúmina ordinaria se divide en porcelana 99, porcelana 95, porcelana 90, porcelana 85 y otras variedades según el contenido de Al2O3 (en referencia al contenido de Al2O3 de 99%, 95%, 90%, 85%, etc.). La principal diferencia radica en el dopaje del sustrato La cantidad es diferente. Cuanto menor es la cantidad de dopaje, mayor es la pureza del sustrato. Existen ciertas diferencias en las propiedades eléctricas y mecánicas de los sustratos cerámicos de alúmina de distinta pureza. Cuanto mayor es la pureza del sustrato cerámico, mayor es la constante dieléctrica y la pérdida dieléctrica. Cuanto menor es, mejor es el acabado del sustrato. A veces, los que tienen un contenido de Al2O3 de 80% o 75% también se clasifican como serie cerámica de alúmina ordinaria.

Entre ellos, la porcelana de alúmina 99 se utiliza para fabricar crisoles de alta temperatura, tubos de hornos refractarios y materiales especiales resistentes al desgaste, como cojinetes cerámicos, juntas cerámicas y válvulas de agua; la porcelana de alúmina 95 se utiliza principalmente para piezas resistentes a la corrosión y al desgaste; porcelana 85 Debido a que a menudo se le incorpora algo de talco, se mejoran las propiedades eléctricas y la resistencia mecánica. Puede sellarse con molibdeno, niobio, tántalo y otros metales, y algunas se utilizan como componentes de dispositivos electrónicos de vacío. La porcelana 75 y la porcelana 95 son materiales cerámicos muy utilizados como sustratos para circuitos de película gruesa. Los sustratos cerámicos para circuitos de película fina utilizan sobre todo porcelana 97 o porcelana 99.
Las principales propiedades de los sustratos de alúmina aumentan con el incremento del contenido de alúmina, pero cuanto mayor es el contenido de alúmina, más difícil es preparar cerámica. La porcelana 95 se cuece generalmente por encima de 1500°C. La temperatura de cocción de la porcelana de 99 alcanza más de 1700℃.
Según el color, los sustratos cerámicos de alúmina están disponibles en tres tipos: blanco, morado y negro. Los sustratos de alúmina comunes son blancos y se utilizan como sustratos para LED, sustratos para circuitos de alta frecuencia, etc. Sin embargo, algunas aplicaciones requieren que el sustrato de alúmina no refleje la luz, lo que da lugar a productos de alúmina negra.
Ventajas de los sustratos cerámicos de alúmina
● Buen rendimiento de aislamiento: El sustrato de cerámica de alúmina tiene un buen rendimiento de aislamiento, que puede aislar eficazmente el circuito y evitar fallos causados por fugas y otros problemas.
● Excelente resistencia a altas temperaturas: El sustrato de cerámica de alúmina puede mantener un rendimiento estable en entornos de alta temperatura, puede soportar el funcionamiento a largo plazo en entornos de alta temperatura, y no es fácil de deformar, ablación u oxidación.
● Alta resistencia y dureza: El sustrato de cerámica de alúmina tiene alta resistencia y dureza, puede soportar una cierta cantidad de presión mecánica y el impacto, y no es fácil de romper o desgastar.
● Excelente estabilidad química: El sustrato cerámico de alúmina tiene una buena resistencia a la corrosión frente a la mayoría de los productos químicos y puede funcionar de forma estable en entornos químicamente agresivos.
● Buen rendimiento de procesamiento: El sustrato cerámico de alúmina tiene un buen rendimiento de procesamiento y se puede utilizar para taladrar, fresar, cortar y otros procesos de procesamiento, y puede lograr formas geométricas complejas y requisitos dimensionales de alta precisión. El procesamiento de circuitos puede llevarse a cabo basándose en la fotolitografía de película fina, y su precisión puede alcanzar el nivel de micras. Se pueden diseñar muchos dispositivos pasivos a partir de sustratos cerámicos de alúmina. Dado que su constante dieléctrica es superior a la de los sustratos generales de PCB, los dispositivos diseñados son de tamaño reducido. Esto supone una ventaja muy significativa en la tendencia de desarrollo de la miniaturización de diversos módulos de componentes.
Aplicaciones de los sustratos cerámicos de alúmina
① Sustrato cerámico para resistencias de chip
Ventajas del sustrato cerámico de alúmina de resistencia: pequeño tamaño, peso ligero, pequeño coeficiente de expansión térmica, buena fiabilidad, alta conductividad térmica y densidad, lo que mejora en gran medida la fiabilidad del circuito y la densidad de cableado del circuito. Es el material portador de los elementos de resistencia de los chips.
② Sustrato cerámico para circuitos integrados híbridos
El circuito integrado híbrido (hydrid) es un método de embalaje que debe contener al menos dos o más componentes, uno de los cuales es activo. Se montan sobre láminas aislantes de cinta conductora metálica que han sido fabricadas con películas gruesas o finas. Los circuitos complejos fabricados con esta tecnología son circuitos integrados híbridos. El sustrato proporciona soporte mecánico al circuito y ofrece un lugar de deposición para los materiales conductores de banda, los materiales dieléctricos y los materiales resistivos que forman los componentes pasivos. También proporciona soporte mecánico para todos los componentes pasivos y activos del chip.
En los circuitos integrados híbridos, los sustratos más utilizados son el óxido de aluminio, el óxido de berilio, el óxido de silicio, el nitruro de aluminio, etc. Sin embargo, teniendo en cuenta el coste y el rendimiento, se utilizan mucho los sustratos de alúmina de gran pureza con superficies lisas. Debido a los distintos contenidos de alúmina, la calidad y el grado del sustrato también varían. Los más comunes son la alúmina 99,6% y la alúmina 96%. La primera suele ser adecuada para circuitos de película fina, mientras que para circuitos de película gruesa, el sustrato de alúmina 96% es el mejor. puede satisfacer sus requisitos de proceso. La cerámica de alúmina cocida multicapa utiliza generalmente láminas verdes de cerámica de alúmina entre 90 porcelana y 95 porcelana como material básico.
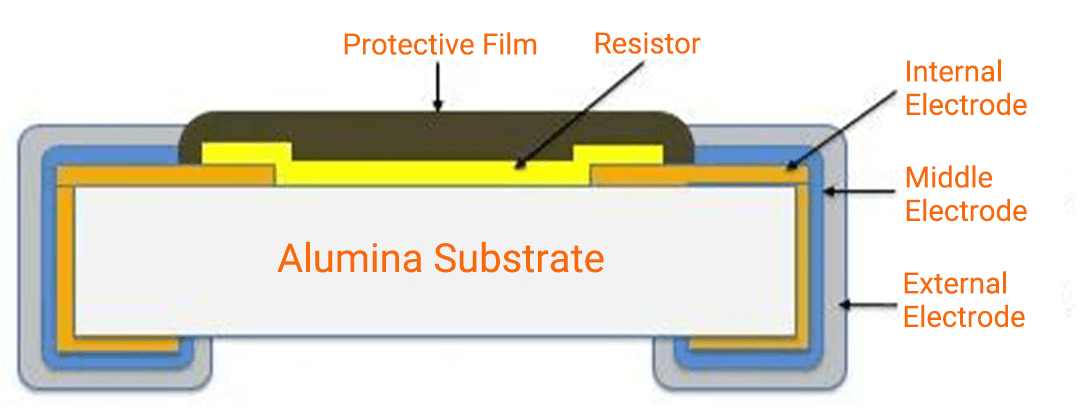
③ Debido a la conductividad térmica relativamente baja de la cerámica de alúmina (20-30W/m-K), los sustratos para dispositivos de potencia no se ajustan bien a los coeficientes de dilatación térmica de los materiales semiconductores como el Si y el SiC, lo que limita el uso de sustratos de alúmina en dispositivos de alta potencia. aplicación.
④ Sustrato cerámico de alúmina para LED
Los sustratos de disipación de calor para LED de alta potencia son principalmente sustratos cerámicos. Los sustratos cerámicos de alta potencia más utilizados en el mercado son los LTCC (cerámicas de cocción a baja temperatura) y los DPC (cerámicas de cobreado directo). Los materiales cerámicos incluyen alúmina, nitruro de aluminio, etc. Los sustratos cerámicos de alúmina para LED tienen las características de alta disipación del calor y alta estanqueidad al aire, lo que puede mejorar la eficacia luminosa y la vida útil de los LED. Su buena estanqueidad al aire los hace muy resistentes a la intemperie y pueden utilizarse en diversos entornos.
Para el envasado de dispositivos electrónicos de potencia, además de la función básica de cableado (interconexión eléctrica), también se requiere que el sustrato tenga una alta conductividad térmica, aislamiento, resistencia al calor, resistencia a la tensión y rendimiento de adaptación térmica. Los sustratos cerámicos metalizados representados por DBC y DPC tienen un rendimiento superior en conductividad térmica, aislamiento, resistencia a la tensión y resistencia al calor. Se han convertido en el material preferido para el envasado de dispositivos de potencia y son reconocidos gradualmente por el mercado. El material de sustrato más común para el envasado de dispositivos es el sustrato de alúmina (Al2O3), que generalmente es un sustrato de alúmina con un contenido de alúmina de 96%. La tecnología del sustrato de alúmina es muy madura y de bajo precio.
Si necesita productos cerámicos industriales, no dude en ponerse en contacto conmigo 0086-17702411651