La tecnología de moldeo por inyección de cerámica, denominada CIM, es una rama importante de la tecnología de moldeo por inyección de polvo (PIM). También se desarrolla sobre la base de una tecnología de moldeo por inyección de polímeros relativamente madura. Como puede fabricar productos con formas complejas y tiene las ventajas de una gran precisión dimensional, una superficie lisa y un bajo coste, se ha desarrollado rápidamente.
Visión general del proceso de inyección de cerámica
La cerámica se divide a grandes rasgos en cerámica de uso diario y cerámica industrial. Aquí presentamos principalmente la cerámica industrial. Hay muchos tipos de cerámica industrial, los más utilizados son alúmina, circonio, carburo de silicio, nitruro de silicionitruro de boro, etc. Las cerámicas industriales suelen tener una gran dureza, resistencia al desgaste y a las altas temperaturas, así como una gran resistencia a la corrosión, por lo que se utilizan ampliamente en electrónica, maquinaria, industria química, aeroespacial y otras industrias.
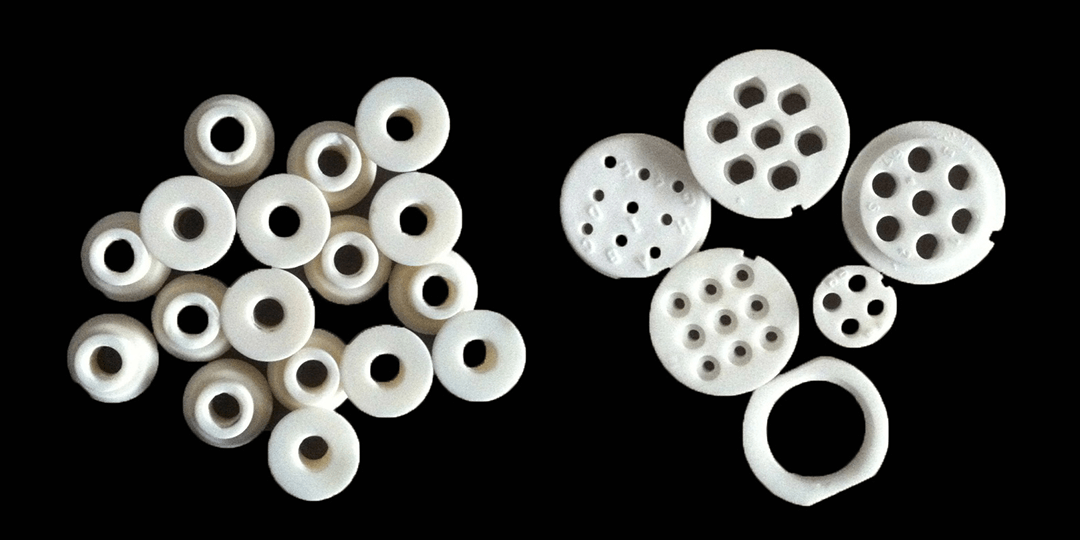
En general, existen tres métodos de moldeo para la cerámica industrial. El primero es el método de fundición; el segundo es el método de prensado en seco; y el tercero es el método de inyección. Aquí presentamos principalmente la tecnología de moldeo por inyección de cerámica (Moldeo por Inyección de Cerámica CIM). Para los diferentes tipos de cerámica, los procesos de moldeo por inyección son similares, y se denominan colectivamente inyección de cerámica a continuación.
El moldeo por inyección de cerámica es un método de preparación de piezas cerámicas con formas complejas y excelentes propiedades mediante la mezcla de polvo cerámico con aglutinantes orgánicos, molienda, mezcla, granulación, alimentación, moldeo por inyección, desengrasado y sinterización. Tecnología de moldeo. Esta tecnología tiene las ventajas de una gran precisión de moldeo y una alta eficiencia, por lo que se ha utilizado ampliamente en el campo de la cerámica.
A continuación se explican detalladamente estos procesos:
▪ Molienda del polvo: Moler el polvo cerámico original para mejorar su fluidez y uniformidad, lo que es beneficioso para el posterior proceso de moldeo por inyección.
▪ Mezcla interna de polvo cerámico y aglutinante plástico: Mezclar el polvo cerámico molido con una cantidad adecuada de aglutinante, y preparar las materias primas de inyección de cerámica fluida a través de la mezcla, el mezclado, el secado y otros procesos en un mezclador interno. Para el moldeo por inyección, los adhesivos incluyen PP, PE, PA, POM, etc.
▪ Inyección de alimentación: Se inyecta la lechada de inyección cerámica en el molde y, mediante procesos como el mantenimiento de la presión, el enfriamiento y el desmoldeo, se obtienen piezas cerámicas con una forma y un tamaño determinados.
▪ Desengrasado: Mediante calentamiento u otros métodos físicos y químicos, se elimina el adhesivo de las piezas cerámicas para obtener un embrión verde con una forma básica.
▪ Sinterización: El embrión verde se sinteriza a altas temperaturas para densificarlo y formar el producto cerámico final.

Selección de máquinas de moldeo por inyección
El adhesivo puede estar hecho de diferentes materias primas, por lo que al seleccionar la máquina, especialmente el tornillo, deben tenerse en cuenta las características de la materia prima cerámica y del adhesivo.
▪ Selección del tornillo y el barril: Aunque los diferentes tipos de cerámica tienen una dureza muy diferente y otras propiedades después de la sinterización, son básicamente los mismos en la etapa de la materia prima antes de la sinterización. Son básicamente muy similares al barro. En términos generales, la proporción de aglutinante No excederá 20%. Estos materiales cerámicos causarán mucho desgaste en el barril del tornillo. Al seleccionar tornillos, es mejor elegir tornillos de acero rápido u otros materiales de carburo y barriles con manguitos internos de aleación a base de níquel. La relación de compresión del tornillo se controla generalmente entre 2,0 y 2,3, la relación longitud-diámetro del tornillo es de aproximadamente 22:1, el extremo delantero del tornillo está equipado con una cabeza de mezcla abierta, y la brida de la cabeza necesita añadir un orificio de ventilación.
▪ Selección de la potencia: A diferencia del moldeo por inyección ordinario, hay procesos de desengrasado y sinterización después del moldeo por inyección de cerámica, especialmente la sinterización. Si la tensión interna del embrión verde de cerámica inyectada es grande, la deformación durante la sinterización también será relativamente grande. Por lo tanto, la elección de la potencia adecuada de acuerdo con el espesor de la pared del producto es un paso clave. En términos generales, elegiremos la potencia de la máquina para que sea mayor que la potencia real requerida con el fin de obtener una mayor velocidad de inyección. En cuanto a la presión de inyección, debido a la poca fluidez de la pasta cerámica, se requiere una presión de inyección relativamente grande.
▪ Selección del tonelaje de la máquina: La gravedad específica de las diferentes cerámicas varía mucho, por lo que sería más científico para nosotros utilizar el volumen de inyección para seleccionar el tipo. Dado que la inyección de cerámica no requiere mucha fuerza de sujeción, siempre que el molde se pueda bajar y el volumen de inyección sea suficiente (la relación entre el volumen de inyección de la máquina y el volumen del producto es mejor entre 3:1 y 2:1), se pueden fabricar productos básicos.
▪ Selección de marcas de máquinas: No hay muchas marcas de máquinas maduras para la inyección de cerámica. En general, se utilizan principalmente marcas como Rigang, Arburg, Jibo y Haitian.
Requisitos del molde
▪ Requisitos para el acero del núcleo del molde: También debido a la abrasividad de la cerámica, el material del núcleo del molde también debe ser de acero aleado con mayor dureza.
▪ Escape del molde: La inyección de cerámica se utiliza para evitar poros en el interior del producto, lo que puede provocar desguaces tras la sinterización. Además, como los adhesivos suelen utilizar POM y otras materias primas que generan más gases, los requisitos de escape del molde son relativamente altos. Al mismo tiempo, como la velocidad de inyección no puede ser demasiado rápida, la ranura de escape debe situarse lo más lejos posible, en el extremo más alejado, donde la cola se desplaza más lentamente.
▪ Canal de moldeo: Debido a la escasa fluidez de los materiales cerámicos, en general no se recomienda utilizar canal caliente, y el diámetro del canal frío debe ser lo mayor posible para facilitar el flujo de las materias primas cerámicas.
▪Puerta del molde: Al igual que en los dos puntos anteriores, para aumentar el flujo de materias primas cerámicas y la necesidad de escape, la compuerta del molde generalmente debe ser más grande.
▪El número de cavidades del molde: Dado que la mayoría de los productos cerámicos tienen ciertos requisitos de tamaño, y puesto que el embrión verde de cerámica todavía se enfrenta a un paso de sinterización después del moldeo, el tamaño de los productos con un gran número de cavidades es a menudo difícil de controlar, por lo que se utiliza generalmente Un plan con un pequeño número de agujeros.

Ajuste del proceso
▪ Velocidad de inyección: en el proceso de inyección de cerámica, una velocidad de inyección demasiado alta puede producir fácilmente defectos como poros y líneas de chorro, mientras que una velocidad demasiado lenta puede provocar problemas como líneas de soldadura. Por lo tanto, se suele utilizar un proceso de llenado lento a través de la compuerta y, a continuación, un llenado a velocidad media. .
▪ Presión de inyección: A diferencia del moldeo por inyección de plástico ordinario, una presión de inyección excesiva puede causar problemas de tensiones internas, que no sólo se refieren a la presión de mantenimiento. Debido a la escasa fluidez de la cerámica, se generarán grandes tensiones internas en determinadas posiciones de pandeo durante el proceso de inyección. El embrión verde moldeado puede no tener problemas, pero una vez sinterizado, estas posiciones producirán mayores tensiones internas. Deformación que dará lugar a la chatarra del producto. Por lo tanto, al inyectar, intente utilizar una presión de inyección más baja. Lo mismo ocurre con la presión de mantenimiento.
▪ Temperatura de fusión: Una temperatura del material más alta es beneficiosa para eliminar la tensión del producto, pero una temperatura del material demasiado alta provocará la liberación de gas y producirá poros y otros defectos, especialmente en el caso de las materias primas cerámicas que utilizan POM con una gran cantidad de gas como aglutinante. .
▪ Temperatura del molde: Una mayor temperatura del molde es obviamente beneficiosa para mejorar la fluidez de las materias primas cerámicas en el molde, reduciendo así la tensión interna del producto. Sin embargo, una temperatura de molde excesivamente alta puede hacer que el plástico utilizado como aglutinante flote hacia la superficie en contacto con la superficie del núcleo del molde, lo que puede afectar a la calidad del producto tras la sinterización.
▪ Velocidad de apertura del molde: Dado que las propiedades físicas del embrión verde cerámico recién formado son todavía relativamente frágiles, la velocidad de apertura del molde debe ser relativamente baja y la vibración debe reducirse al máximo. Lo mismo ocurre con la extracción robotizada.
Si necesita productos cerámicos industriales, no dude en ponerse en contacto conmigo 0086-17702411651